All you need to know about integrated steel plant | MS Life
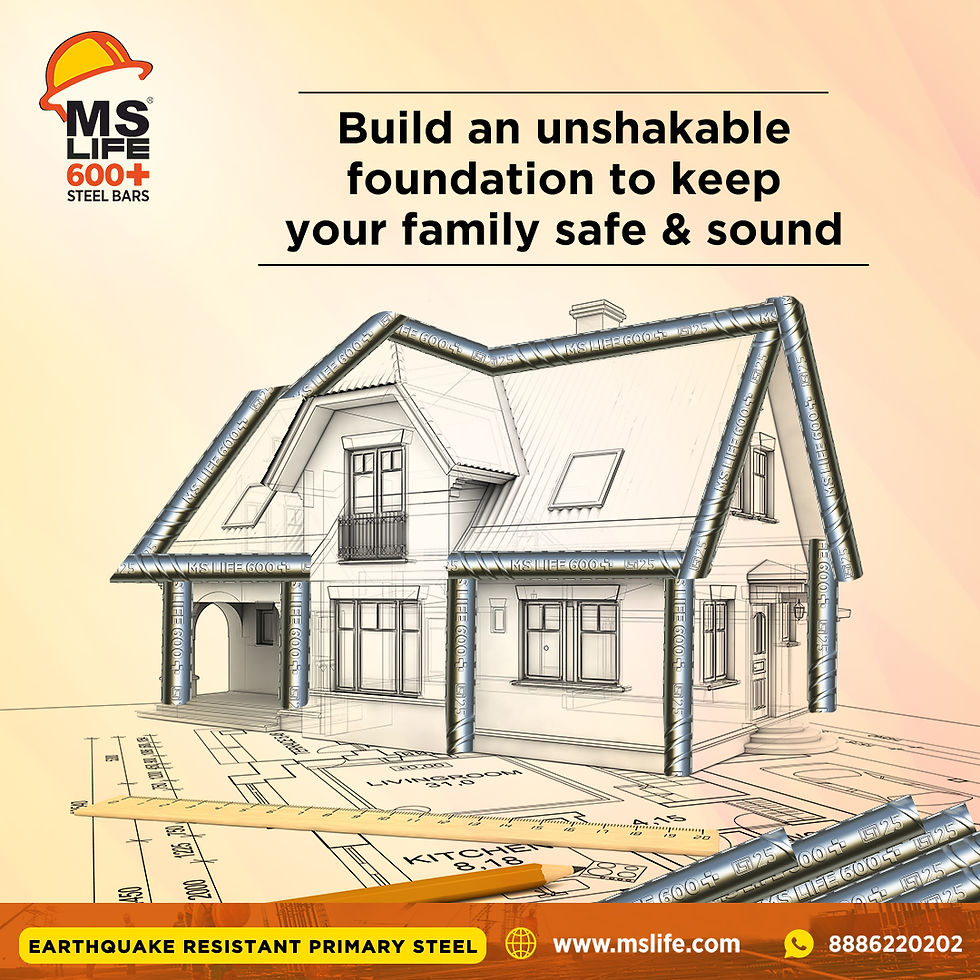
An integrated steel plant, also known as a steel mill or steelworks, is a large-scale industrial facility that manufactures steel from iron ore. It is called "integrated" because it combines various processes and facilities in a single location to produce steel efficiently. Here's what you need to know about integrated steel plants:
Raw Materials: Integrated steel plants typically utilize three primary raw materials: iron ore, coal or coke, and limestone. Iron ore is the primary source of iron, while coal or coke provides the necessary carbon for the ironmaking process. Limestone acts as a flux to remove impurities during ironmaking.
Ironmaking: The first major process in an integrated steel plant is ironmaking. It involves the reduction of iron ore in a blast furnace, where the iron ore, along with coke and fluxes, is fed from the top. High-temperature reactions occur, resulting in the production of molten iron, known as hot metal or pig iron.
Steelmaking: After ironmaking, the molten iron undergoes steelmaking processes to convert it into steel. In the BOF process, oxygen is blown into the hot metal to remove impurities and adjust the carbon content. The EAF process uses electric arcs to melt scrap steel and/or other iron sources, along with additives, to produce steel.
Continuous Casting: The molten steel produced in the steelmaking process is then cast into solid shapes using continuous casting. In this process, the liquid steel is poured into a water-cooled copper mold, which solidifies it into continuous lengths of steel, typically in the form of billets, blooms, or slabs.
Rolling and Finishing: The solidified steel is then sent to rolling mills for further processing. The rolling mills shape the steel into various forms such as sheets, plates, coils, bars, rods, and structural sections. These processes involve hot rolling, cold rolling, and heat treatment to achieve the desired dimensions, mechanical properties, and surface finishes.
By-Product Utilization: Integrated steel plants often have facilities to recover and utilize by-products generated during the steelmaking process. For example, blast furnace gas, a by-product of ironmaking, can be used as fuel in various plant operations. Slag, a byproduct of steelmaking, can be processed and used in construction materials.
Auxiliary Facilities: Integrated steel plants require a range of auxiliary facilities to support their operations. These include power plants for providing electricity, water treatment plants, coke ovens for producing coke from coal, and various material handling and storage facilities.
Integrated steel plants are complex and capital-intensive operations that require significant investments in infrastructure, machinery, and skilled labor. They play a crucial role in meeting the global demand for steel and are often key contributors to local economies. MS Life is one of the best integrated steel plants in South India that produces the best quality TMT bars for your dream construction..
Recent Posts
See AllCalculating the quantity of TMT bars for your construction project is a crucial step to ensure structural integrity and...
Comments